Garments Dyeing: Garment dyeing is a process of imparting color materials to fully fashioned garments like as shirts, pants, twill garments, jackets, pullover, T-shirt, Polo shirt, sweaters etc. The garments are usually dyed before finishing with various trimmings or accessories. In textile coloration it is not so far initiated in our country but it is more popular outside our country like as France, Italy, Spain, Germany, Canada, North America, turkey, Israel, Japan, USA, Uk, China etc.

Garment dyeing is an opposition of the conventional method of making garments from previously dyed fabrics. Knitted fabrics, twill weave fabrics and/or other woven fabrics made from cotton yarns are subjected to garment dyeing. Garments made of cotton material are easy to dye up but besides cotton several other fabrics can be found in whole or partially made of wool, silk, nylon, polyester or acrylic are subjected to garment dyeing.
Dip Dyeing: In garments dyeing, dip dyeing is becoming more popular day by day as the fashion trend and customer demand. Due to cheap and easy process it is as popular to the manufacturers. It is also as called gradient dyeing. It is the process, the fully fashioned garments are arranged to dip into a dye bath (vessel, bucket, bowl etc) accordingly a pre-determined area or height. This process runs again and again. According to demand, garments are to be soaked into dye bath up to a certain limit for enough time. To dye up the garment as deeper shade to light shade from bottom to top the gradient time will be maintained for certain area of the garment.
Process flowchart for DIP Dyeing
- Scouring (80°C)
- Neutralization (With Acetic Acid)
- Enzyme (At 45°C Temp and PH-4.5-5.5)
- Dyeing (90°C Temp for 3-5 Minutes)
- After Treatment (Fixing Agent)
- Softener (Commercial Softening Agent)
- Bath Drop

Normally garment dyeing runs with two types dyestuffs available in the market.
1. Direct Dyes
2. Reactive Dyes
a) Hot Brad
b) Cold Brand
For dip dyeing we use direct dye though it has low color fastness property, moreover it takes less time for color fixation
Necessary Items:
- Dye Bath ( Vessel, bucket, bowl or any other container)
- Hanger
- Washing Machine
- Stirrer
- Rubber gloves
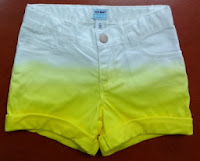
Pretreatment: As the fabric is not ready for dyeing after making cloths, it is treated with caustic soda and peroxide solution to perform pretreatment process which helps to make it more absorbent and free from natural color as well as other impurities.
Recipe:
- Caustic Soda (NaOH)-2gm/l
- Per-Oxide (H2O2)-4gm/l
- Detergent-1gm/l
- Temp-80°C
- Time-15min
Working Procedure: A lot of garments are now taken into the dyeing machine for easy performing the pretreatment process (Good to know that, scouring, dyeing or any normal wash can also be done into a washing machine). Now add Caustic Soda, Hydrogen peroxide and Detergents according to the above recipe. Now maintain the liquor ratio at 1:10 at 80°C. Now perform this treatment for 15 minutes. Well scoured garments are treated as more absorbent, where color permanency will be high. In this process the garments are to be more absorbent, removing the natural or unwanted colors to make genuine white, oils as well as other impurities. Good scouring plays an important role during dyeing, color fastness and appearance. The whole materials are now subjected to rinse wash to remove the caustic and other chemicals. Now the garments are neutralized with Acetic Acid so that any of the caustic soda does not exist with the material. The PH of Acetic acid should be kept into 4.5 to 5.
Note: If the garments are made with zipper of cotton tape frequently be torn during the scouring process, so nylon or polyester tape is recommended to use here.
Enzyme: After scouring process the full quantity of garment needs to treat with enzyme which will help to remove the hairiness and projectile fibers as well as make the garments ready for dyeing. You can use Acid enzyme as 2gm/l at 45-55°C for 15 minutes. After enzymatic treatment one or two rinse wash to be done for washing it properly. (PH during enzymatic treatment keeps in 4.5 to 5)
Recipe: We have used this for dyeing 380 Pcs baby girls shorts.
- Direct Dye-355gm
- Salt (Glubar Salt)-10gm/l
- Labeling & Wetting Agent-1gm/l
- Water-2500L
- Temp-95°C
- Time-5min
Working Procedure: Make the dye bath ready with direct dye as normal dyeing procedure. At first we will be sure the garment is made from scoured and bleached fabric, otherwise scouring or pre treatment will have to complete. After adding dyes, salt and wetting agents it needs to stir to make the dye bath properly. For getting more color fastness and reduce fixation hours we can use some binding agents as we need. The temperature of dye bath remains around 90-95°C.
The garment which is used to dyeing need to attach with hanger or something else to hang it from, then water uses to wet the garment properly before taking it underneath the dye bath. Now start to place the garment into the dye bath as desired height. You may require helps in doing this so as not to spill the dye everywhere. Once the garment has been soaking in the dye bath for long enough time then remove it carefully so that color spot does not transfer to the non-dyed portion. If so, run the garment, from non-dyed section to dyed section, under warm water until water runs clear. This will remove any excess dye from the garment. Continue the process till your desired shade is developed and maintain the shade at different areas of the garment. To get as deeper to lighter shade at bottom to top you can soak the garment into dye bath as long enough time. The process of dip dyeing is not so crucial but it takes extra precautions, care and many more times. During dyeing it will take spraying some water to the garment to wet it and helps to absorb colors by the material.
Once your desired shade produced it needs to take it into a washing machine.
After Treatment: It is the process usually doing after dyeing for color fixation and color permanency as well as improving the color fastness. This is a chemical treatment so as for this a typical recipe is given below.
Recipe:
- Commercial Fixer-0.5gm/l
- Softener (Cationic)-0.5 gm/l
- Temp-40°C
- Time-3-5 minutes
- M:L ratio- 1:10
Working Procedure: After completing the dyeing it will be required some process to have sufficient dye molecules penetration to the most inner part of the fibers. In the dye bath now adds the fixing agent (Commercial Fixer) according to the recipe. Temperature in this bath will keep at 40°C and treatment time is 3-5 minutes. By this treatment the material will be treated as finally colored. Most of the dye particles will finally enter into the core of fibers and the fiber will swell at some extent so that the pores of fibers will be reduced and dye materials cannot come out from the innermost part. It will increase the color fastness of the materials. Before this treatment is started a rinse wash will be done to remove extra dyes which adhere with the materials and after this process also another rinse will be done to remove unfixable dyes or sediment dyes at the bottom of the dye bath. Now softener is added to the bath to make the material softer, improving hand feel and brightness.
Now just hanging up the garments for 20 minutes to squeeze extra water (Do not use hydro extractor to reduce staining or uneven color adhering). You can use oven to dry the garments as well, you can get prominence color performance without staining or shade variation. Now the garments are cured at curing chamber at 150-200°C to dry finally and properly. You can use dryer for a while at the final stage.
Over Dyeing in Garments: When a fully fashioned garment is dyed for another color though it can be used as wearing dress, this technique is so called over dyeing. Usually coloration is performed over a consisting color on to a garment is referred as garments over dyeing. As an example when a purple colored fully ready garments are supposed to be subjected for red color it may call as over dyeing. There is a common concept among the garments trade peoples, when a garment is dyed with its whole area is known as garments dyeing but when color imparts fully or partially over garments can be defined as garments over dyeing, because it could be used as wearing dress before this coloration. In garments dyeing normally two types of dyestuffs are used such as Direct Dye and Reactive Dye. The garments which are required to dye up should be made of cotton fiber though many of them are now produced with combination of other fibers as blends. Dyeing procedure of over dyeing is as like as other normal dyeing arrangements but here some extra precautions and care must be taken. At present the garments washing plants are capable to make the garments over dyeing. If the garments which are white in color and can use as dress are subjected for dyeing is also known as over dyeing.
Garments Tie Dyeing: Tie means make a knot to garments different places as if they cannot come in contact with dyes or chemicals during dyeing. It is as like as batik printing method. A garment is tied at different places prior to dyeing; as a result whole garments will be colorful remaining the tied places un-dyed. Indeed this technique is known as garments tie dyeing and now is becoming so popular in the world garments trade.